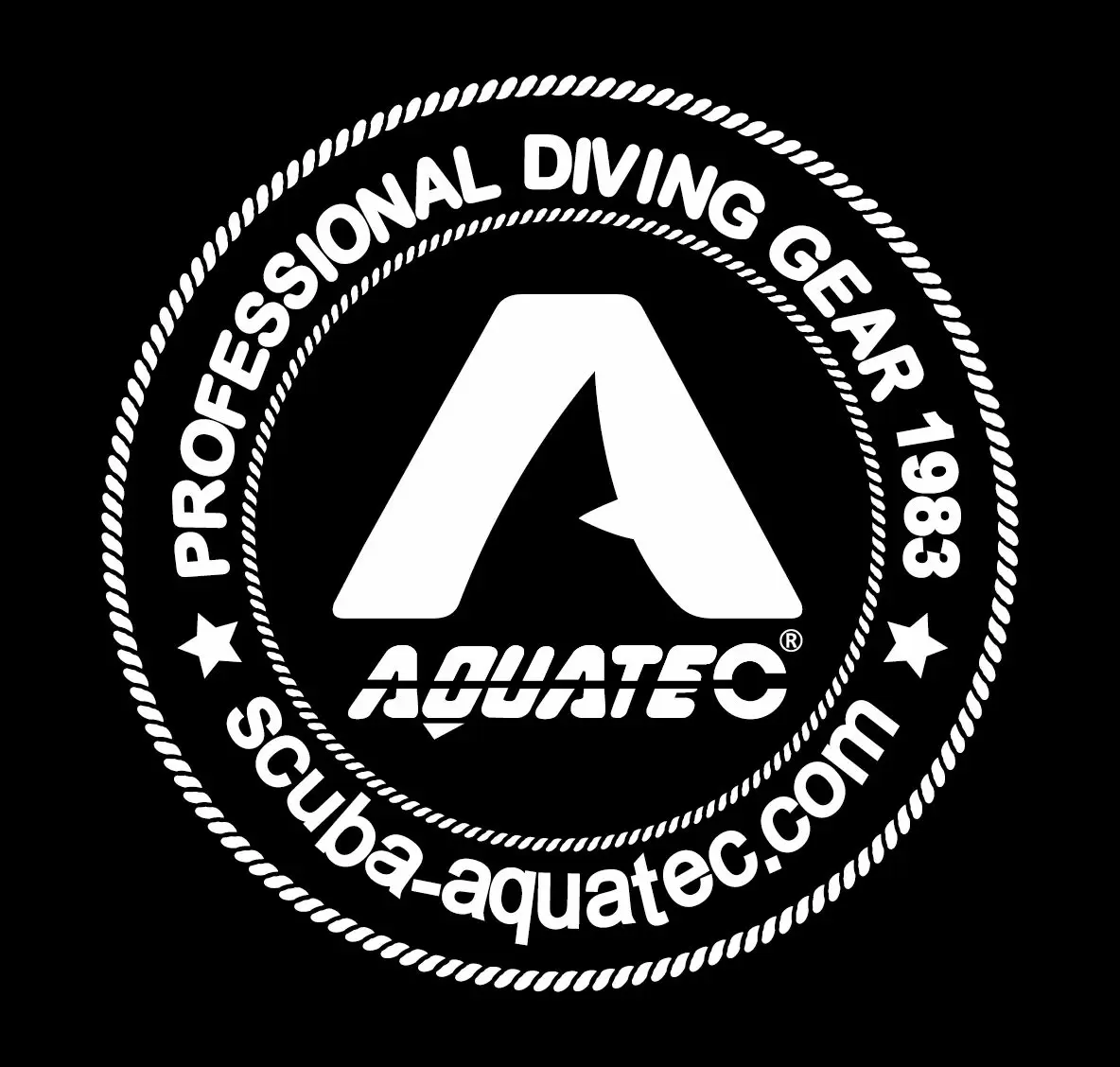
生產流程

接到業務單位確認完成之「受訂單」,由生管轉成「生產訂單」,並建立時程管制表,經產線生產及品質檢驗,確實管制生產時程。
組裝與檢驗過程中依《品質檢驗管制程序》管制執行,確保作業及產品品質。
為縮短客戶等待出貨的時間,由生管依照訂單數量規劃生產預計時間,有效管控產品安全存量,使出貨時程縮減到最短。
料件、資料之鑑別及追溯
生產過程中所產生的料件、半成品,均以《5S管理法則》規範擺設辦法,明確標示品名、規格、製造編號及當時存放之狀態等,避免料件遺失或誤用。
生產檢驗過程均依「產品檢驗記錄表」內之檢驗項目執行相關紀錄作業,由工程師於該項完成後簽名或蓋章以示負責,大項之產品均登入產品編號以利往後進行售後服務作業時可追溯產品相關紀錄。
所有產品由ERP、PDM等管理系統確實掌控各式產品的料件清單完整記錄,以達最高售服效率。
廠務相關規範
生產過程中使用之機器設備維護保養,依《設施環境維護程序》執行辦理,以確保生產及售服過程不受不良環境以及器具影響現場作業強調對產品的保護;為避免不當的碰撞而造成產品外觀的瑕疵,所有承托產品的車輛及器具,均以《5S管理法則》規範來巧思設計防撞/防刮的措施。
避免產品受陸運/海運/空運顛簸影響,而造成外箱破裂/產品損傷等狀況發生!外箱是以五層瓦楞紙設計,增加荷重強度;高單價之產品再以精美彩色盒/真空植絨包裝;使包裝結構無懈可擊。每一外箱盡量不以超過30公斤為原則以利客戶端搬運儲藏。